第1章:業務改善がもたらす3つの変化
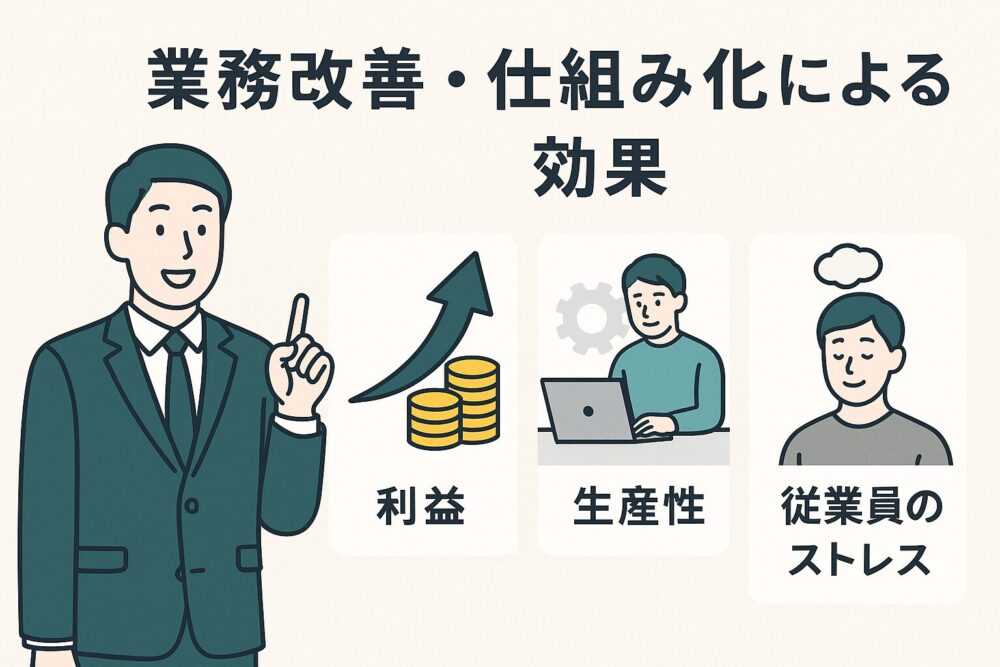
スーパーの現場では、日々やるべきことに追われて「業務改善」にまで手が回らない…そんな声をよく耳にします。
しかし、実はほんの少しの見直しや仕組み化で、現場は大きく変わるのです。
ここでは、業務改善によってもたらされる3つの大きな変化について解説します。
利益が上がる
業務改善を行うと、まず無駄なコストを削減できます。
例えば「在庫の適正化」や「発注ミスの削減」は、直接的にロスや廃棄を減らし、利益を押し上げます。
また、「手戻り」や「二度手間」がなくなることで、少ない人員でも回る体制が作れ、人件費の圧縮にもつながります。
生産性が上がる
無駄に歩く・探す・やり直すといった作業が多いと、それだけで時間が消耗します。
動線や備品の配置を見直すことで、生産性が上がります。
従業員のストレスが減る
業務改善による最大のメリットは現場のストレス軽減です。
「どこに何があるか分からない」「やり方が人によって違う」などのストレスを根本から取り除けます。
第2章:スーパーの現場に潜む「非効率」の正体
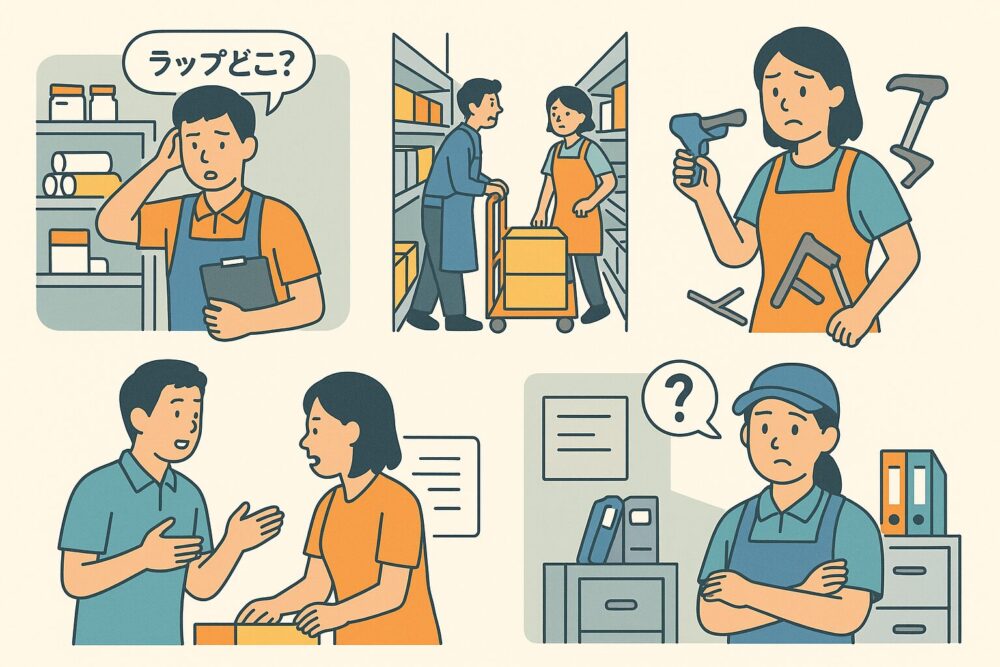
「人が足りない」「忙しくてミスが多い」「新人が育たない」などの悩みの原因は、非効率の積み重ねです。
在庫や備品の置き場がバラバラ
探す時間・移動・確認などが作業ロスにつながります。
通路が狭く、作業がしにくい
作業動線が悪いと時間のロスが積み重なります。
道具や設備の使いづらさ
古い機器や使いにくい道具は作業効率を下げ、リスクを高めます。
情報の属人化と共有不足
共有されていない情報は、ミスや二重対応の原因になります。
マニュアルの不在 or 古くて使えない
誰が教えるかで内容が違うと、教育にムラが出ます。
第3章:生産性を一気に上げる「動きやすい売場」づくり
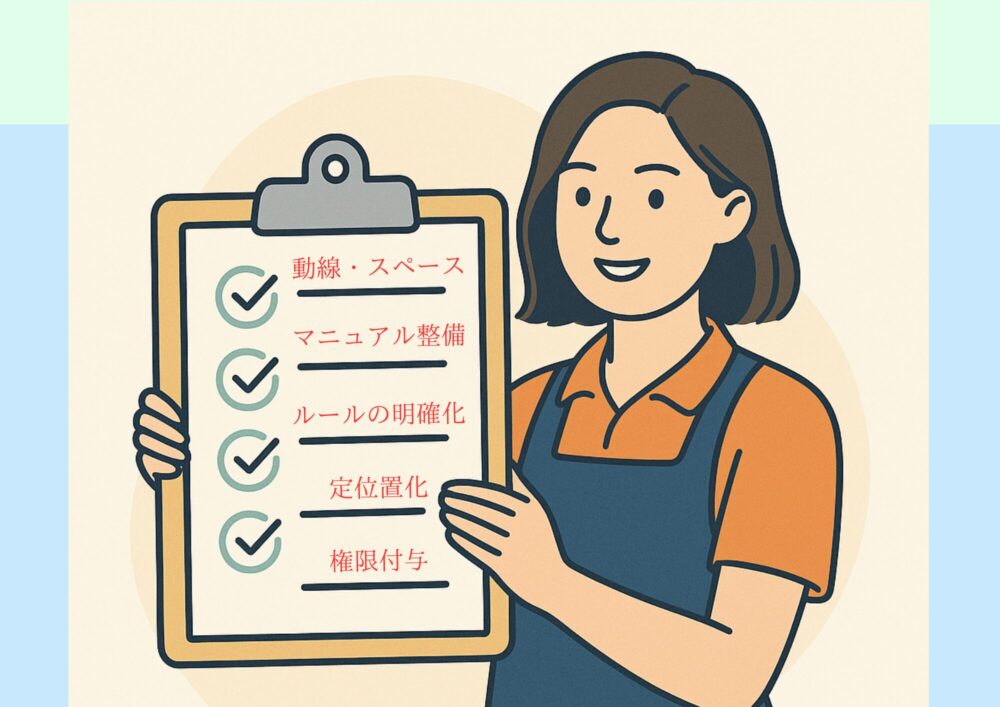
通路幅と動線の最適化
人や台車が通りやすい配置が必要です。
備品・在庫の定位置化
探す時間を減らす工夫が必要です。
エリアごとの作業ゾーンの明確化
作業・在庫・販売ゾーンの役割を明確に。
機械・道具の導入と最適活用
ハンディ・台車・チェックリストなどを活用。
第4章:仕組み化の第一歩は「NGルールの明文化」から
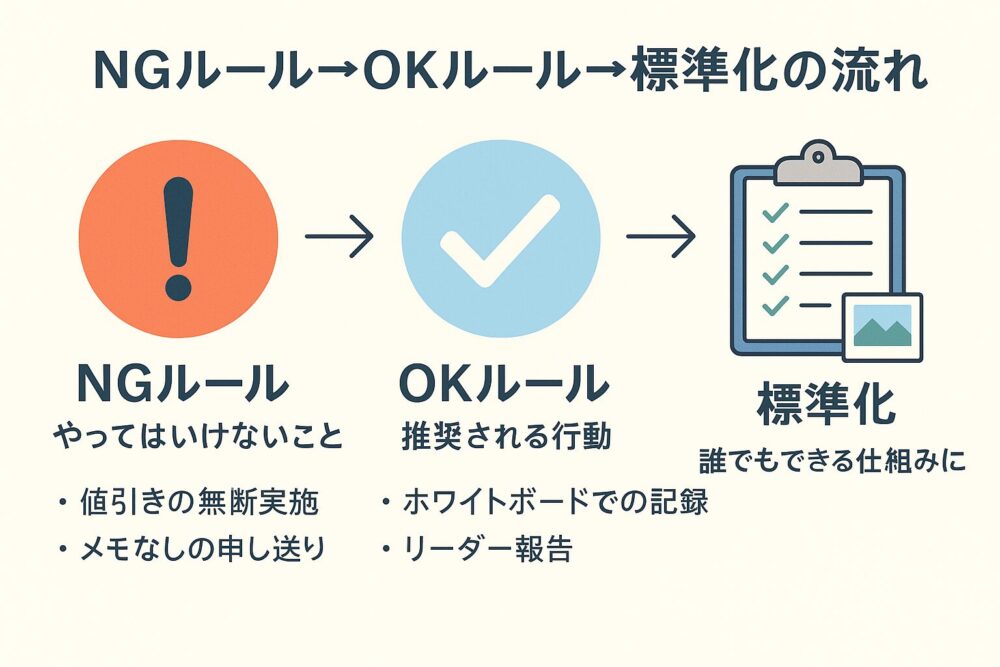
暗黙の了解をなくす
明文化で失敗を減らし、安心感を生む。
NGルールがあると心理的安全性が生まれる
「やってはいけないこと」があると迷わず行動できる。
NGルール→OKルール→標準化の流れ
ルールは段階的に浸透させるのがコツ。
NGルールは5つまでに絞る
覚えやすさが継続の鍵。
第5章:人が活きる仕組み ― スキルに応じた役割と権限の設計
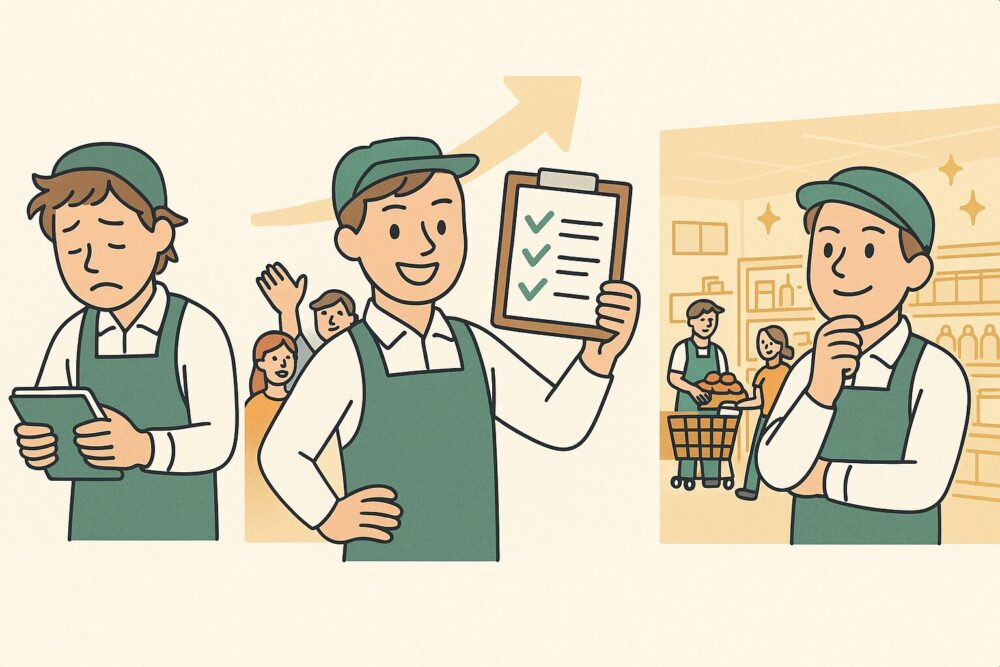
なぜ役割と権限の設計が必要なのか?
誰に何を任せるかで現場のストレスが変わる。
スキルマップを作ろう
作業内容と担当者の見える化が鍵。
判断権限を明確にする
どこまで判断してよいかを明文化。
権限は“信頼”で育てる
育成と任せる勇気が重要。
スキルの広がりが改善スピードを加速させる
誰でも対応できる体制が現場を守る。
第6章:誰でもできる!業務改善→仕組み化への4ステップ
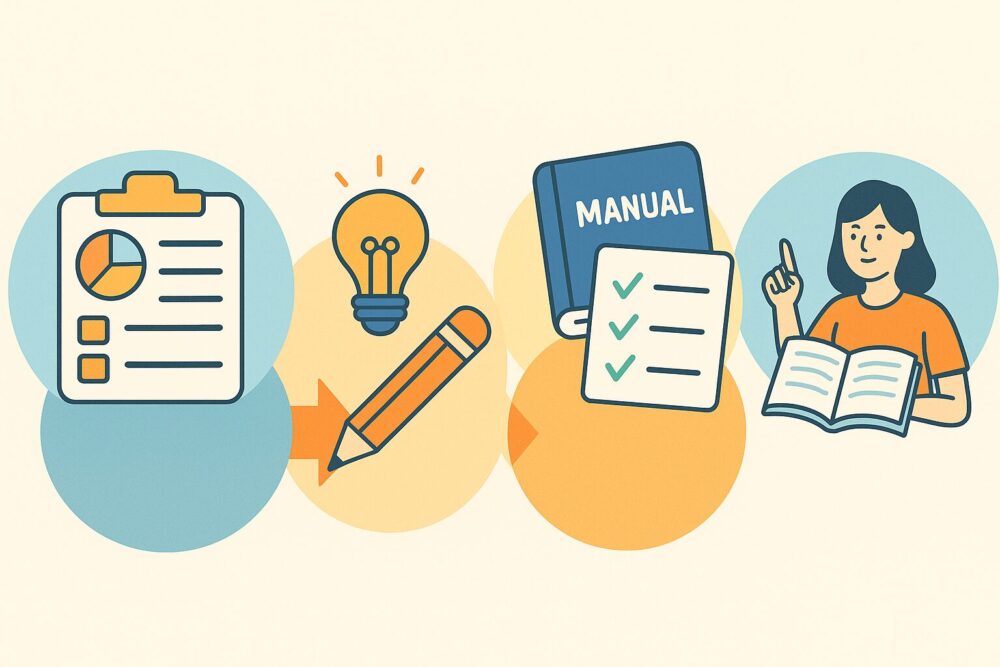
- 業務の見える化
- 改善点の洗い出し
- 標準化(マニュアル・チェックリスト化)
- 教育・定着
第7章:現場で成果が出た“改善のリアル事例”
事例①:パック破損による22.6日分のロス削減
返品処理11分 × 年間988パック = 約181時間 → メーカーにパッケージ改善提案 → ロス削減成功!
事例②:レジ袋の受け渡し改善で1日100分の時短
レジ袋の確認・手渡しをストッカー導入で省略。1人60秒 × 100人で1日100分の時短!
第8章:成果最大化!仕組み改革チェックリスト
導入編チェックリスト
- ムダの洗い出し
- 動線改善
- NGルール
- スキルマップ
- 権限設計
定着編チェックリスト
- 改善報告
- 成果の見える化
- マニュアル更新
- 数値記録
- 店長の旗振り役としての行動
改善は“がんばる人を守る仕組み”であり、現場を強く、優しくしていく力です。
コメント